Global Supply Chain
Quality, responsiveness, and efficiency are the cornerstones of our supply chain. Our approach is based on our simple objective of providing solutions and spare parts according to our customers’ needs, at the right cost and quality, and delivered to the right place at the right time in a sustainable way.
The Global Supply Chain team at Marel is responsible for procurement, manufacturing, and logistics within the company. With more than 2,700 team members, we support the innovation, manufacturing, and distribution of standalone equipment, full-line solutions, and spare parts for poultry, meat, and fish processing.
Our Innovation, Manufacturing, and Service teams co-operate closely to provide the best products and services for our customers. Whether we’re investing in new technology, developing our sites to increase efficiency, or providing equipment and spare parts, we deliver and service according to our customers’ specific requirements. We achieve all of this through close co-operation with our key suppliers, partners, and distribution network.
Despite shortages and other logistical challenges due to the pandemic, we had good performance on equipment deliveries in 2021. This was made possible by the continuation of our co-location strategy to optimally produce in cost-effective locations, and by strong collaboration between our Procurement and Planning teams across the different manufacturing sites. Currently, we have 15 manufacturing sites for equipment and spare parts that can support our extensive service platform.
In 2021, the need for Marel’s innovative solutions, software and services continued to rise, mirrored in 22% rise in orders received in 2021. Revenues however were only up 10% and therefore we recognized the need to ramp up. We took major steps toward our goal of generating 50% of our revenues from software, service, and spares by 2026. We have made organizational changes at key spare parts production facilities through separating the inventory of spares from equipment. Further, we’ve continued setting up dedicated Order Fulfillment teams to handle spare parts orders to provide better visibility in our delivery process.
Marel is a trusted maintenance partner, building strong and long-standing relationships with our customers. This is reflected by two sequential record quarters in spare parts revenues. Our Global Supply Chain supports our strategy and growth plans while prioritizing business continuity for all our customers.
Safety, quality, and sustainability
Safety, quality, and sustainability are always our priorities, and in 2021 we further strengthened our processes in these areas. During the pandemic, we remain committed to best practices in all locations to safeguard our employees, customers, and other contacts.
Best practices include general measures, such as wearing masks and social distancing, as well as measures tailored to our factory environment, such as staggering shift patterns, disinfecting tools and workstations between shifts, and setting up physical barriers on the factory floor to section off the space into smaller cells, minimizing contact between employees.
TRACK system expanded
With our internally developed safety and quality concern management system TRACK now fully implemented in Global Supply Chain, we were able to record and avert incidents better across our manufacturing locations. We have met and exceeded the set target for reporting of hazardous situations, with a 16% increase in reporting compared to 2020. This reporting is crucial in the prevention of recordable incidents and first aid cases.
During the year, we continued development of the TRACK system and expanded it to include Service and Innovation. The implementation in these functions will continue in 2022 and will allow any feedback from Service to flow directly to Global Supply Chain and Innovation, and vice versa.
Minimizing nonconformities
As part of our accreditation to the Quality Standard ISO 9001 and the Weights and Measures Certification to sell scales in the market, our locations in Colchester in the United Kingdom and Gardabaer in Iceland were audited several times during 2021. On each occasion, both facilities successfully passed the audit with no nonconformities observed.
Resolution time of nonconformities and concerns in 2021 across all types of issues has decreased by 17% when compared to 2020. Specifically, for our customer detected issues, we have seen a decrease in resolution time of 44% compared to 2020.
Supplier sustainability platform
Our focus on sustainability and responsible procurement continued in 2021 with the implementation of the EcoVadis platform. This widely recognized platform provides supplier sustainability ratings and allows companies to assess the environmental, social, and corporate governance (ESG) performance of their global suppliers. We have assessed our own rating and have started to invite our top suppliers to get rated as well. This effort will continue in 2022. More details on our ESG efforts can be found in the Sustainability chapter.
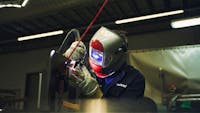
Optimized manufacturing through co-location
Marel is always looking to expand and upgrade its facilities to be close to customers all around the world. Together with our four main distribution centers, we now run 15 manufacturing sites for equipment and spare parts that support our extensive service platform.
Good deliveries despite various pandemic related challenges were possible due to the flexibility provided by our co-location strategy, an integral element of our supply chain strategy.
Co-location involves producing mature products in optimal cost locations, rather than innovation centers or so-called mother-sites. This has four main benefits: It moves production nearer to our customer base, reduces production costs, increases distribution capacity and flexibility, and spreads risks in case of natural disasters or trade barriers. We are continuing co-location to our plants in Brazil, the US, China, and Slovakia to be close to customers and optimize cost levels.
As part of this strategy in 2021, we significantly increased our capacity for assembly in Nitra in Slovakia, and will invest and expand our facilities in the next two years in addition to increasing efficiency and implementing a second assembly shift. We also successfully piloted and are now rolling out digital assembly instructions. This not only reduces the risk of errors but also allows less experienced team members to follow instructions and illustrations from a screen, reducing the training time required.
We’ve taken further steps for co-location across the globe in Guaporé, Brazil. The objective was to enable our customers in the region to access local government financing (FINAME) by purchasing Marel equipment manufactured and sourced within Brazil. The first product to be co-located as part of this strategy was the SmartLine grader. In December 2021 the SmartLine manufactured in Brazil was successfully approved as being eligible for FINAME financing. Further products will be co-located for manufacturing in Guaporé, Brazil in 2022.
During 2021 we also invested in upgrading the assembly facilities in Colchester in the United Kingdom, and parts manufacturing in Boxmeer in the Netherlands and Stovring in Denmark. New standards will be incorporated into all our future manufacturing infrastructure projects, creating bright and inspiring workplaces in all our manufacturing centers.
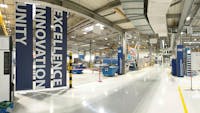
Did you know?
Major growth at Marel Nitra
In November 2020, Marel celebrated 15 years since opening its manufacturing facilities in Nitra, Slovakia. During that time, Marel Nitra has developed and grown tremendously. Starting with only nine employees in 2005, the location has now around 420 employees.
Nitra is one of our 15 production sites and one of more than 30 Marel locations around the world. The Nitra facilities include a large modern office space as well as Marel’s largest assembly manufacturing facility worldwide, or around 18,000 m2. As part of our co-location strategy, the Nitra facilities and team produce products that have graduated from the development phase and have become standard products.
Assembling hours in Nitra are estimated to increase to 250,000 in 2022 and to 280,000 in 2023, up by approximately 25% from the current capacity and an almost nineteen-fold increase from 2010. By 2023, Nitra will represent about a quarter of the total assembly capacity of Marel’s manufacturing facilities worldwide.
Automating and digitalizing to improve speed and scale
Continued investments in our manufacturing platform will be a key enabler for Marel’s organic growth target. We are strengthening our foundation for growth and scalability with high levels of automation, digitalization, and a low environmental footprint in line with our sustainability goals.
There are opportunities to automate and digitalize the backend to shorten lead times and prepare for the future growth curve ahead, where the largest investments are expected in spare parts handling and changing the flow in the factories.
Over the next four years, Marel will focus investments to better support the global reach and aftermarket capabilities. We will advance the supply chain, invest and improve our distribution network for spare parts. Further, we will bring some of the key manufacturing locations to the next level with a focus on modern ways of working, including improved automation and use of robotics.
Official customer commentary indicates that our customers are stepping up in capital expenditures to increase automation, strengthen agility in market channels and stock keeping units (SKUs), and improve safety and sustainability. Changes in consumer behavior are affecting our customers, and we need to change our behavior accordingly to support flow in projects and aftercare business that is becoming more dynamic and demanding in terms of delivery times.
These enhancements of our manufacturing platform and parts handling facilities will ensure that we can deliver the right quality, at the right time, at the right cost and in a sustainable way to our customers.
Procurement
A semiconductor and logistics crisis set in swing by the pandemic has led to severe supply shortages worldwide. These shortages impacted Marel and its suppliers in many categories throughout the year. In response, we have established additional structures and actions to ensure availability of products to our customers.
As of the beginning of 2021, mitigation actions in place have included close co-operation with our suppliers to solve bottlenecks, and increased commitment toward suppliers by ordering ahead. As is clearly reflected in our financial statements, we are also keeping higher inventory levels for critical components.
We are also working closely with Innovation to re-design alternative components when needed, and with Manufacturing to reschedule production depending on availability of parts. We have set up, next to local dedicated teams, a global allocation team to optimize the allocation of components across sites, and a dedicated global team to search for missing components in the broker market.
These responses are governed by a global risk management team, and agile problem solving is facilitated by cross functional teams per site. We have succeeded in minimizing the impact of the crisis through very strong co-operation between all Marel disciplines and suppliers.
Spare parts
Continuing our journey to carve out the spare parts supply chain starting in 2019, we are working to further strengthen our position as the trusted maintenance partner for our customers. This ongoing journey is reflected in the rise in service and spare parts revenues as a proportion of our total revenues.
In 2021, we took the next major steps in reaching our objective, by splitting the inventories for spare parts and equipment at key spare parts production facilities. This allows us to plan our inventories to meet the specific needs for manufacturing and spare parts, respectively. This is relevant both in the procurement strategies and the reliability and transparency of inventories to both supply chains.
We have also continued with the organizational set-up of dedicated Order Fulfillment teams in Europe, after already having gone live with our team in North America in 2020. These teams act as ‘spiders in the web’ with a sole focus on spare parts orders.
Several activities centered on streamlining and rationalizing our end-to-end processes, and master data and performance measurements are ongoing with dedicated teams. This is not only to increase our current performance but also to support the next steps in our spare parts journey.
In Europe we are preparing our largest future transformational project supporting an automated and digitalized physical fulfillment process. All of this is to support our ambition of having 50% of our revenues generated by software, service, and spare parts in 2026.
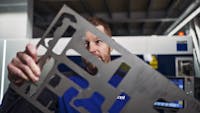
Logistics
We have increased our focus on logistics within Marel. To ensure that our customers are receiving the best logistical care in a consistent way, we’ve strengthened our ways of working toward a standard global approach.
As many other companies have experienced, logistics costs increased during the year, and in parallel a higher degree of inaccuracy in transit times developed.
One of the actions that we have taken is to reduce the number of carriers that we are working with. This allows us to establish strategic partnerships with global carriers and helps us with better cost management and level of capacity commitment from carriers.
During 2021, we have also been working on getting the logistics activities of our latest acquisitions included into existing carrier contracts, resulting in significant freight cost savings for these locations.

Did you know?
3D metal printing project and acquisition of machine
In May 2021, Marel decided to invest in a 3D metal printer for the production of stainless steel products. The new 3D manufacturing technique, also known as Additive Manufacturing (AM), offers many new opportunities for Marel. The machine was purchased and installed in Boxmeer in December 2021, a revolutionary step in supporting our Innovation department, regular production, and spare parts.
The project is the result of close co-operation between Marel’s Global Supply Chain and Innovation teams. Together with external parties, these teams have conducted many investigations, preparations, and alignment sessions over the last years to ensure a well-founded purchase. The fully operational system is printing 3D stainless steel parts for all Marel sites around the world.
With the investment and exploration of this new technology, we aim to ensure a shorter time to market by decreasing lead times for development and testing, and creating combinations of parts and shapes that we would otherwise not be able to produce.